28.4.2025 / Lecture de 4 minutes
Système de transport intelligent pour les nouveaux matériaux énergétiques : Innovation collaborative des ascenseurs à mouvement alternatif et des transporteurs à chaîne à plaques
Aperçu du projet
This reciprocating elevator is specifically designed for the sealed transport of positive and negative electrode materials for new energy batteries (such as lithium cobalt oxide, graphite, etc.), serving the production lines and warehousing logistics of new energy enterprises. The equipment achieves automated docking of pallets through a high-precision plate chain conveyor system, supporting vertical transport across multiple floors (3 layers with 3 stations).
It has a maximum load capacity of 1500 kg, a lifting height of up to 16.5 meters, and an operating speed of 40 m/min. Its fully sealed structure, corrosion-resistant materials, and intelligent control system meet the requirements for pollution prevention, explosion protection, and efficient transfer of new energy materials. Additionally, it integrates safety protection mechanisms to ensure the stability and reliability of transporting high-value materials.
Paramètres de base -
Category | Parameters |
---|---|
Device Parameters | |
Charge nominale | 1500 kg |
Vitesse de levage | 40 m/min |
Hauteur de levage | 16.5 m (3 layers: 6.5m/10m/16.5m) |
Vitesse horizontale | 0~20 m/min (variable frequency) |
Puissance du moteur | 15 kW |
Structural Parameters | |
Installation Size | L2700 × L2500 mm |
Dimensions de la cargaison | W1800 × L1800 × H2500 mm |
Pallet Dimensions | W1400 × L1400 × H2000 mm (including pallet) |
Docking Method | External roller conveyor (W1500 × L1600 mm) |
Système de contrôle | |
Drive Method | Variable frequency motor + energy-saving main motor |
Méthode de positionnement | Positionnement photoélectrique + détection infrarouge |
Operating Interface | PLC control + touch screen |
Mécanismes de sécurité | Safety clamps + speed limiter linkage, polyurethane buffer, dual limit switches, emergency stop device |
Le défi
Harsh Environment Adaptation: Positive and negative electrode materials are corrosive, requiring equipment to be rust-resistant, sealed, and capable of withstanding dusty environments.
High Precision Docking Requirements: Pallets must seamlessly connect with the plate chain conveyor, with a positioning error of ≤2mm to prevent material tipping.
Safety and Explosion Prevention: Materials like lithium cobalt oxide are flammable, so the equipment needs to be designed with anti-static and explosion-proof features.
Multi-Floor Coordination: Transport across three floors requires synchronized coordination of vertical lifting and horizontal conveying rhythms.
Efficiency Bottleneck: Traditional manual handling cannot meet the automated production line rhythm of 30+ pallets per hour.
Solutions
Corrosion-Resistant Sealing Design: The cargo compartment and rollers are made of 304 stainless steel with a polyurethane coating, and sealing strips block dust, making it suitable for corrosive environments.
Precision Positioning System: Photoelectric sensors combined with PLC closed-loop control ensure that the docking accuracy between the pallets and the conveyor line reaches ±1mm.
Inherent Safety Protection: Explosion-proof motors, grounded static-dissipating rollers, and inert gas-filled cargo compartments eliminate explosion risks.
Intelligent Dispatch Logic: Variable frequency coordination across three layers and three stations, linked with the production line through a WCS system, allows for dynamic priority allocation of pallets.
Efficient Automation Integration: The roller conveyor automatically loads and unloads cargo, with high-speed lifting at 40 m/min, supporting continuous operation for 24 hours.
Avantages
Zero Pollution Transport: Fully sealed cargo compartment with positive pressure clean design ensures material purity.
Haute efficacité: Speed of 40 m/min with automated docking boosts efficiency by 300% compared to manual handling.
Extended Lifespan: Heavy-duty guide rails with a 15-year corrosion-resistant structure reduce maintenance costs by 40%.
Conformité en matière de sécurité: Certified to GB/T 27546-2011 industrial standards, supporting dual protection for emergency stop and overload.
Flexible Expansion: Compatible with AGV and MES system integration, accommodating future capacity upgrade needs.
Galerie
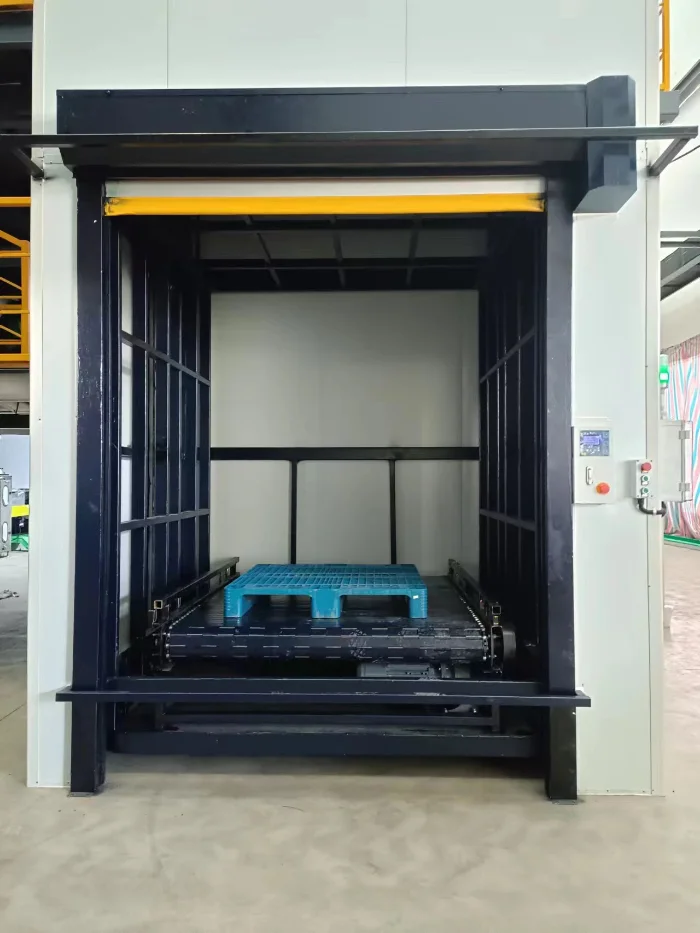
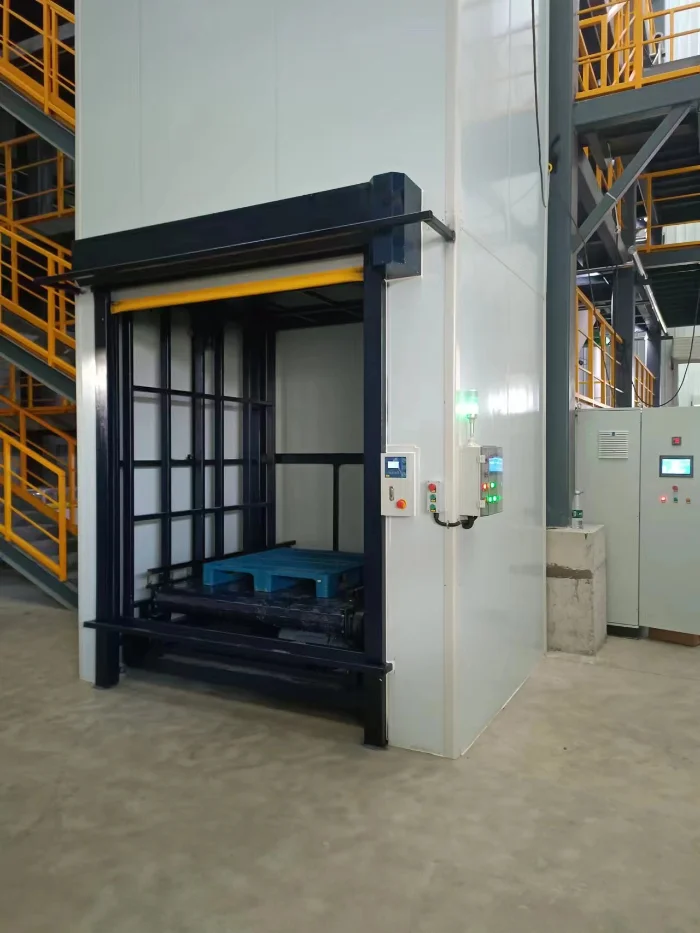
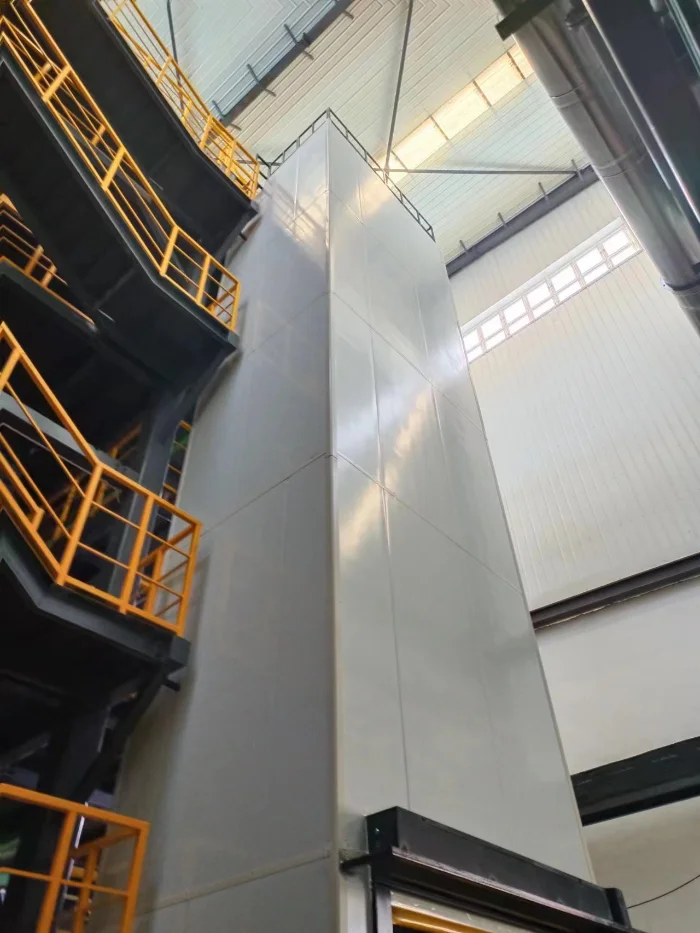
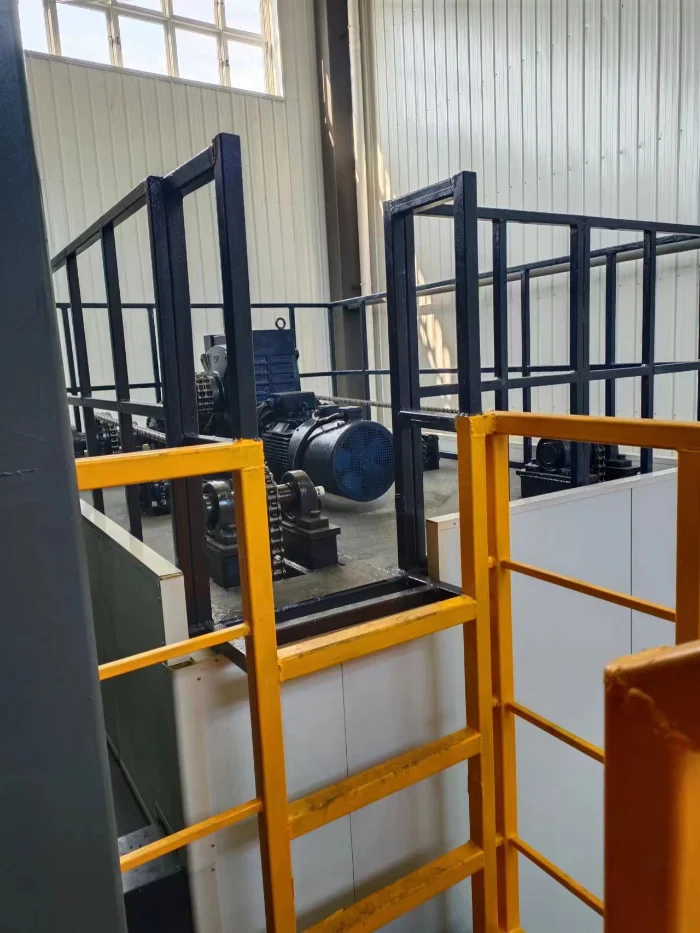