Continuous Vertical Conveyors(CVC)
The CVC enables rapid vertical transport of cartons, pallets, luggage, barrels, and more between floors. With compact Z/C/E configurations, it achieves speeds up to 30m height while reducing footprint by 90% compared to spiral conveyors.
To find out more talk to our team
Minimalist design with enclosed drive, fewer moving parts, easy installation, and reliable operation.
Enables 3D material transfer, adaptable to diverse loads and environments.
Smooth multi-floor transport with automated sorting, minimizing space and energy use.
Integrates with horizontal conveyors to reduce manual handling and boost productivity.
Want to know more? Our helpful
team are here to help.
Request a quote
View our range of Circulating Vertical Conveyors
Conveying capacity: 1500 boxes/hour
Lift height: up to 16m
Lifting speed: ≤ 40m/min
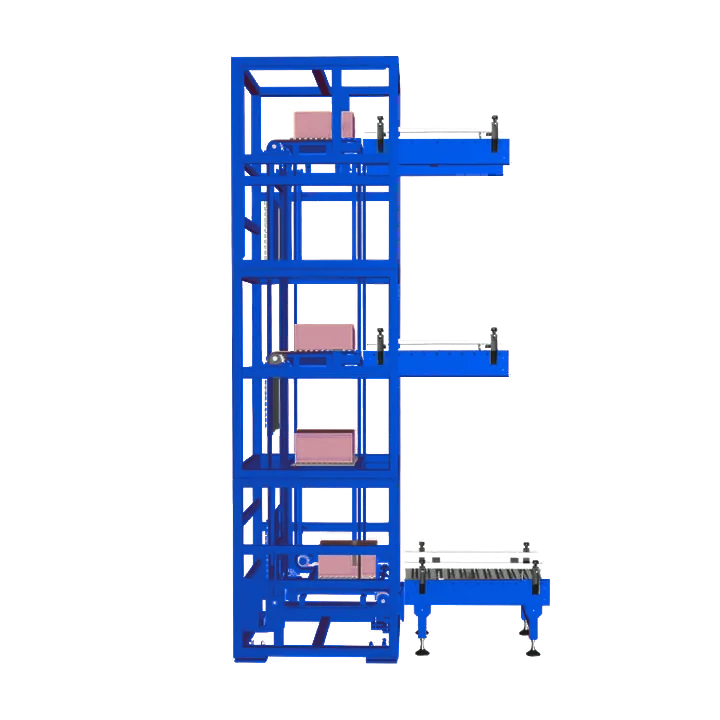
Conveying capacity: 1500 boxes/hour
Lift height: up to 16m
Lifting speed: ≤ 40m/min
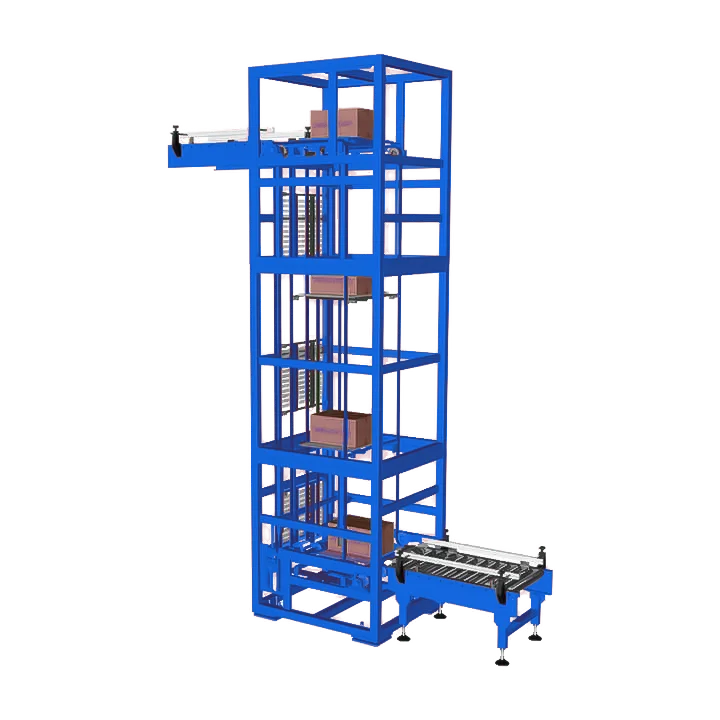
It is combined with the import and export conveyor lines to form a complete continuous lifting system, realizing multi-floor, multi-in and multi-out automated operations, saving space and improving efficiency.
Capacity: ≤ 600kgConveying capacity: 30pcs/min
Lift height: Customized
Size: Customized
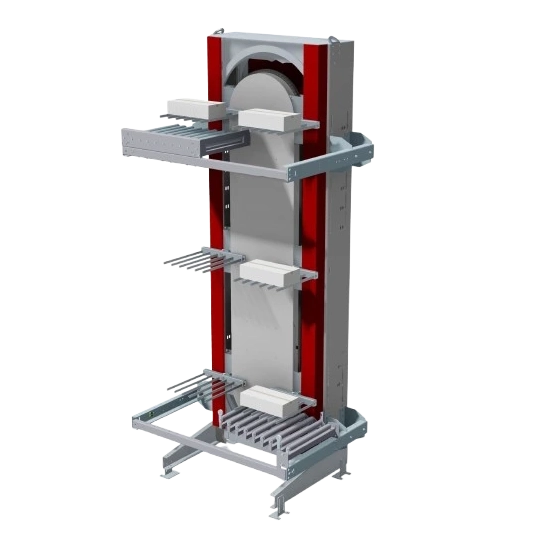
CVC frequently asked questions
Installing a Circulating Vertical Conveyor (CVC) generally requires limited structural modifications. Modular designs adapt to existing spaces, but key factors include floor load capacity, ceiling height, and anchor points for stability. Multi-story setups may involve floor penetrations, though compact Z/C/E-shaped configurations reduce spatial disruption. For tall systems (e.g., 30+ meters), reinforced supports or beams might be necessary to handle heavy loads.
Pre-installation assessments by engineers are critical to ensure compliance with building codes and optimize integration. Electrical and control systems must align with facility infrastructure, but pre-engineered CVCs often minimize structural changes compared to traditional systems. Planning focuses on balancing operational needs with minimal architectural impact.
CVCs prioritize energy efficiency through advanced engineering. Variable-frequency drives (VFDs) dynamically adjust motor speed to match real-time load demands, cutting energy consumption by 20-30% compared to traditional systems. Closed-loop mechanisms reduce mechanical friction, while regenerative braking in high-capacity models recovers kinetic energy during downward cycles. Automated idle modes further minimize power use during operational pauses.
Lightweight aluminum frameworks and modular designs lower inertial resistance, enhancing long-term sustainability. Though energy use varies with load weight and vertical height (up to 30+ meters), CVCs outperform spiral or belt conveyors in lifecycle efficiency. Reduced maintenance needs—thanks to fewer moving parts—also contribute to lower operational costs, aligning with eco-conscious facility goals.
CVCs are engineered for material versatility. Customizable carriers with adjustable clamping systems securely transport fragile goods like glassware or electronics. Soft-start/stop controls and vibration-dampening mechanisms prevent jostling, while optical sensors detect unstable loads and trigger speed adjustments. For irregular shapes, modular attachments like expandable trays or magnetic holders ensure safe vertical transit.
Exceptionally bulky or asymmetrical items may require tailored solutions, such as robotic arm integration for precise loading. Most standard CVC configurations support weights up to 2,000 kg and item sizes within 2m x 2m dimensions. Pre-installation consultations help optimize system parameters for specialized handling needs in industries like aerospace or luxury packaging.